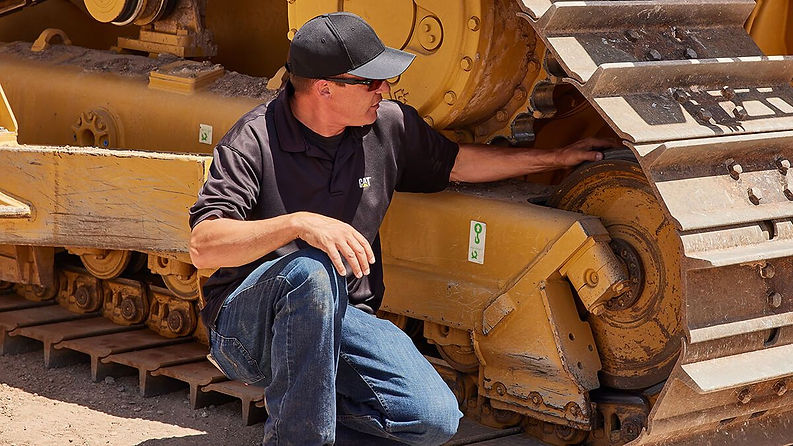
Caterpillar Wear Management - Enhancing Equipment Longevity Through Digital Innovation
Principal UX/UI Designer and Digital Strategist
01

Project Overview
The Caterpillar Wear Management service is a comprehensive digital solution designed to optimize the maintenance and longevity of heavy equipment. Comprising a web application for dealers, a mobile app for field inspectors, and an innovative ultrasonic probe device, this service enables precise tracking and management of equipment wear, preventing costly unscheduled downtime.
02
Problem Statement
Unplanned equipment failure poses a significant risk to productivity and can lead to substantial financial losses. The challenge was to develop a system that enables proactive maintenance planning, ensuring equipment reliability and operational efficiency.

03

My Process
-
Research and Strategy: Initiated the project with extensive research into dealer and customer pain points, focusing on the need for a reliable maintenance planning tool.
-
Design and Prototyping: Led the design of the web and mobile applications, focusing on user-friendly interfaces that allow for easy monitoring of equipment wear and maintenance scheduling.
-
Integration of Technology: Spearheaded the user experience integrating ultrasonic probe technology into the service, enabling precise wear measurements directly in the field.
-
User Testing and Iteration: Conducted rigorous testing with dealers and field inspectors to refine functionalities and ensure the platform met all user requirements.
04
Solutions & Key Features
​
-
Web Application for Dealers: Allows dealers to monitor customer fleets, track equipment configuration, and manage wear conditions and maintenance schedules.
-
Mobile App for Field Inspectors: Facilitates on-site inspections, enabling inspectors to record measurements, take photos, and make notes on equipment wear, which can be directly reported to customers.
-
Ultrasonic Probe Integration: A cutting-edge tool that measures the metal thickness of equipment components, providing accurate data on wear and remaining lifespan.
-
Report Generation: Automated report generation feature that compiles inspection data into comprehensive reports for customer review.
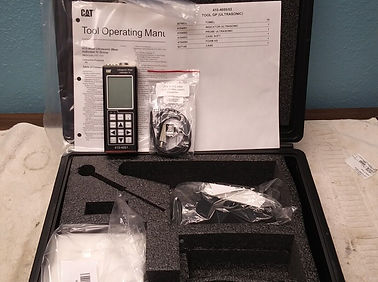
Service Blueprint

06
Tools & Techniques
-
Tools Used: Utilized Figma for UX/UI design, and collaborated with engineering teams using Agile methodologies for the software development lifecycle.
-
Techniques: Employed user-centered design principles and Lean UX for rapid prototyping, testing, and iteration, ensuring the service meets the high standards of functionality and user experience.

07

Recognition
Cat WMS is recognized as the leading digital services application to enable the organizational growth challenge of $28 Billion in revenues for aftermarket components by 2026.
08
Reflection
This project underscored the importance of integrating digital tools with physical devices to solve complex industry challenges. It highlighted the value of close collaboration between designers, engineers, and end-users in creating solutions that significantly impact operational efficiency and customer satisfaction.
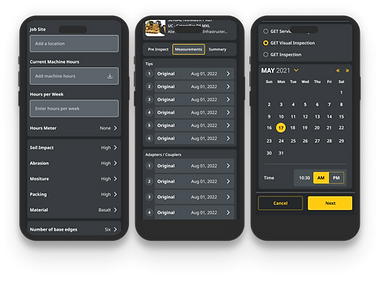